News Archiv 2018-EN
Malaysia has found its Volvo Trucks Fuelwatch Challenge 2018 champion, Haree Murughan Muniandy from ASTRO Productions Sdn Bhd. The results were announced during a celebratory dinner at Volvo Trucks’ Port Klang dealer, where nine of the country’s best truck drivers gathered for the results of the competition.
He received a RM 5 000 Bank Simpanan Nasional voucher and a trophy, however, the highlight of his victory is that he will be representing Malaysia in the Volvo Trucks Driver Challenge Global Final in Gothenburg, Sweden later this year.
Following in second place was Hidayu Sabaran from Nittsu Transport Service (M) Sdn Bhd, and at third place was Mohd Harun Mohd Yusop from Fima Freight Forwarders Sdn Bhd.
Volvo Trucks Malaysia Managing Director, Mitchell Peden said Haree had successfully embodied the core purpose of the Fuelwatch Challenge, which is intended to promote safe and fuel-efficient driving among truck drivers.
Volvo Trucks’ annual Fuelwatch Challenge is aimed at promoting maximum fuel efficiency and proper driving skills among truck drivers, through a challenging competitive platform. The competition is open to drivers across Malaysia with two separate categories namely the closed category and the open category.
An overjoyed Haree said as a professional truck driver, he had always admired the effort Volvo Trucks puts into educating drivers on the importance of fuel efficiency and safety in all aspects of driving. “After participating in the Fuelwatch Challenge Finals for the third time, the challenge has not only allowed me to further develop my skills and knowledge, but it also taught me to never give up until I have achieved my goal.”
The winner was determined by the best combination of fuel efficiency (measured using Volvo Trucks’ telematics system called Dynafleet), productivity and safety whilst also demonstrating that they had the ability to handle the different trucks.
This year also marked the first time since the inception of the Fuelwatch Challenge in Malaysia, where a female truck driver made it into Top 3. Hidayu exceeded her own expectations in the challenge. “I have received a lot of support from my friends and family, and I hope my achievement will be an encouragement for all Malaysian women who want to join the trucking industry.”
However, it was last year’s challenge that saw the record being set, when Junaidah Ibrahim made it into the finals, inspiring female participation in this year’s challenge and resulting in eight female truck drivers taking part in the qualifying stages.
Peden said: “This is indeed a proud moment for female truck drivers in Malaysia. Hidayu and Kamila Mohamad Ribi both demonstrated the skills required to drive a truck efficiently and safely is not gender-limited. Female truck drivers have the same ability as their male counterparts to drive at a high skill level on a competitive stage.
“We hope that these talented women will serve as examples of how gender is a non-issue when it comes to driving and I hope that in the future, we will see more talented women participating and potentially winning the Fuelwatch Challenge here in Malaysia.”
Qualification rounds in June and July saw 1 550 driver-participations nationwide, with only the top nine finalists gathering in Shah Alam for the final round.
Also present during the dinner of the Fuelwatch Challenge prize giving ceremony was Dato’ Nazari Akhbar, Executive Director of Taipanco Sdn Bhd, who received seven units of Volvo FH13 trucks in a vehicle handover ceremony. To date, Taipanco has received 17 units of trucks from Volvo and this handover marks the first time that the company is adding the FH model into their fleet.
The handover of the 2 largest PALFINGER loader cranes in Malaysia, the PK150002, took place at Putrajaya Marriot Hotel in Selangor, Malaysia, on the 26th of July, in a joint effort between Palfinger Asia Pacific and their dealer, KTC Crane & Equipment. The event gathered over a hundred customers, operators, as well as KTC’s partners and suppliers.
Customers also took the opportunity to get to know the various other equipment brought to the event venue. This included a P240A Access Platform, a T26A Hookloader, a PK8500, and the reliable workhorse – the PK 32080.
The PK150002 handed over to Mr Ngiam from Curio Pack Sdn Bhd featured a G-boom on a Scania truck while the one handed over to Mr Ngam from Metro Logistics crane featured an E-boom on a Nissan truck.
The PK150002 features a maximum hydraulic outreach of 21.5m and a maximum lifting capacity of 30000kg, with essential features which enhance performance such as the Paltronic 50, AOS, Radio Remote Control, and HPLS.
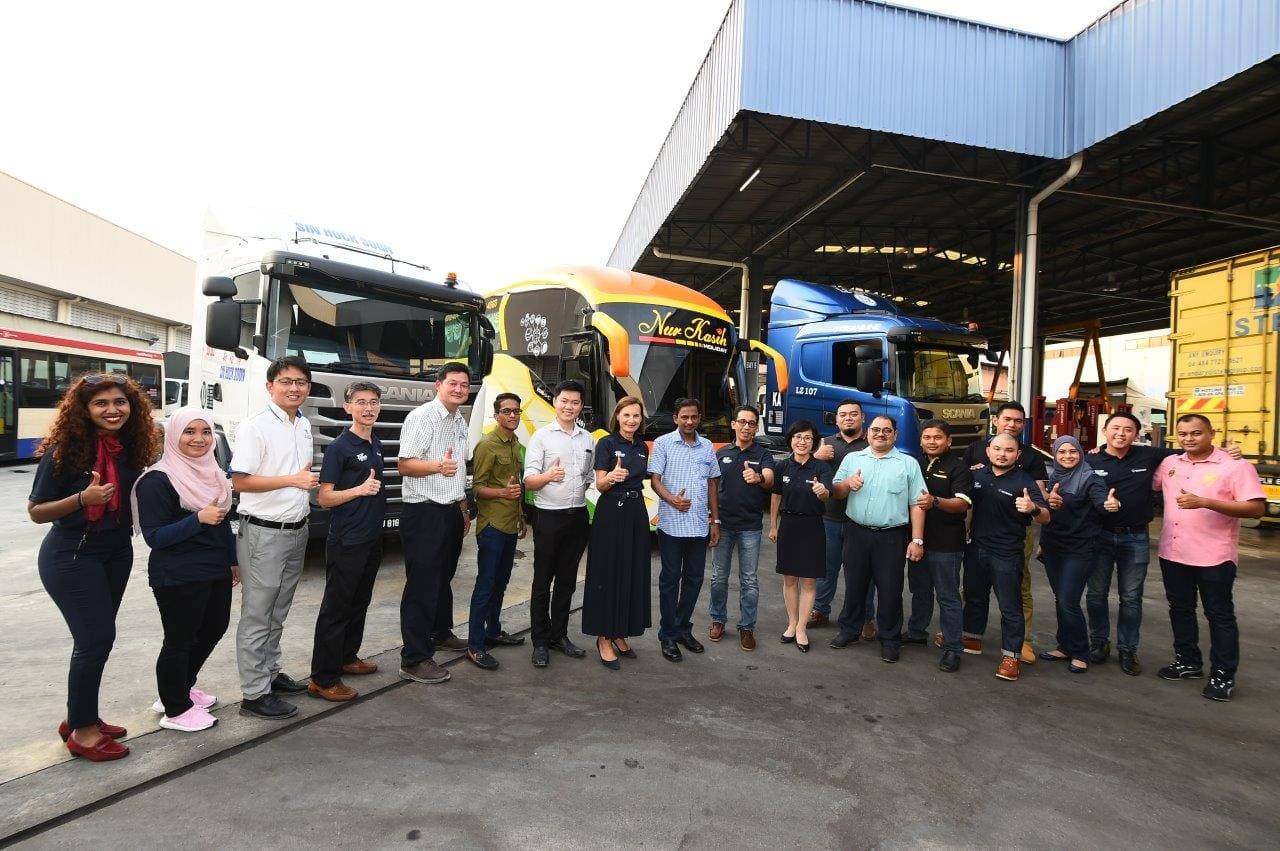
The handover of vehicles was held in conjunction with the Scania Open Day, which served as an opportunity for staff and their immediate family members as well as customers to mingle, understand what Scania can offer as an employer and have a more intimate look at how the company operates.
The IVECO Daily is celebrating 40 years of pushing the boundaries of innovation, versatility and efficiency in light commercial vehicles. Since it was first launched in 1978, it has introduced groundbreaking innovations that have changed the industry: from the adoption of a truck-derived chassis with rear traction and independent front suspension, to the introduction of Common Rail technology in 1999 – a world first – or the advanced Electronic Stability Program (ESP) for regulating vehicle handling during steering and braking.
Over the years since its launch, the Daily has constantly evolved to meet the changing needs of customers, always remaining true to its DNA. It has led the way with its efficient and environmentally friendly technologies, as these demands have become increasingly critical to the transport sector. To this date, it is ahead of the industry in sustainability with the unique concept of the Daily Blue Power: a vehicle family that frees transport operators from the constraints of the strictest environmental regulations and was awarded the title of “International Van of the Year 2018”. The more than 3 million Daily vehicles, manufactured on 3 continents, which are on the roads in 110 countries are testament to this family’s popularity and exceptional capacity for adapting to meet the specific needs of our customers across the world.
Pierre Lahutte, IVECO Brand President, commented: “This year we are celebrating an important milestone in the life of the Daily – a family of vehicles that has been ahead of the industry right from its beginning, and 40 years on is spearheading the industry’s transition to sustainable transport. Throughout its long history, it has enjoyed enormous success with transport operators and industry experts alike, reaping numerous awards across the world. It is a vehicle family that has always looked to the future, and has known how to anticipate our customers’ needs while remaining true to its core values of versatility, reliability and efficiency – always the perfect partner for our customers’ business and environmental sustainability.”
Today the Daily is a vehicle at the forefront of the industry, with a success built on its historical strengths that make up its DNA – starting from its unique chassis frame, which gives it the robustness and versatility it is known for. The load-bearing structure with ‘C’ shaped, special steel cross-members, is the best platform for bodybuilders to adapt for the most diverse missions – including special vehicles such as motorhomes, couriers, waste collection, tippers, cranes, public services, tow trucks, ambulances. It has gained recognition for its unique features, such as rear wheel drive and the 4x4 version.
It offers the widest line-up in the industry ranging from 3.3 right up to 7.2 tonnes of gross vehicle weight, and from 7.3 m3 up to 19.6 m3 cargo volumes. Its advanced features use technology to push the boundaries of performance, raise comfort to a new level, deliver more connectivity and lower its Total Cost of Ownership, reflecting its Business Instinct and making it the perfect business partner.
With the Blue Power Family, it leads the way in sustainability, anticipating the future with the most advanced diesel and alternative traction technologies: the Daily Euro 6 RDE 2020 Ready, the first LCV ready for 2020 Real Driving Emissions regulations; the Daily Hi-Matic Natural Power, the first CNG vehicle with an 8-speed automatic gearbox in the LCV industry; and the zero-emissions Daily Electric. This family offers the perfect solution for unlimited delivery in urban and suburban missions, opening round-the-clock access to city centres with the strictest noise and emissions abatement regulations.
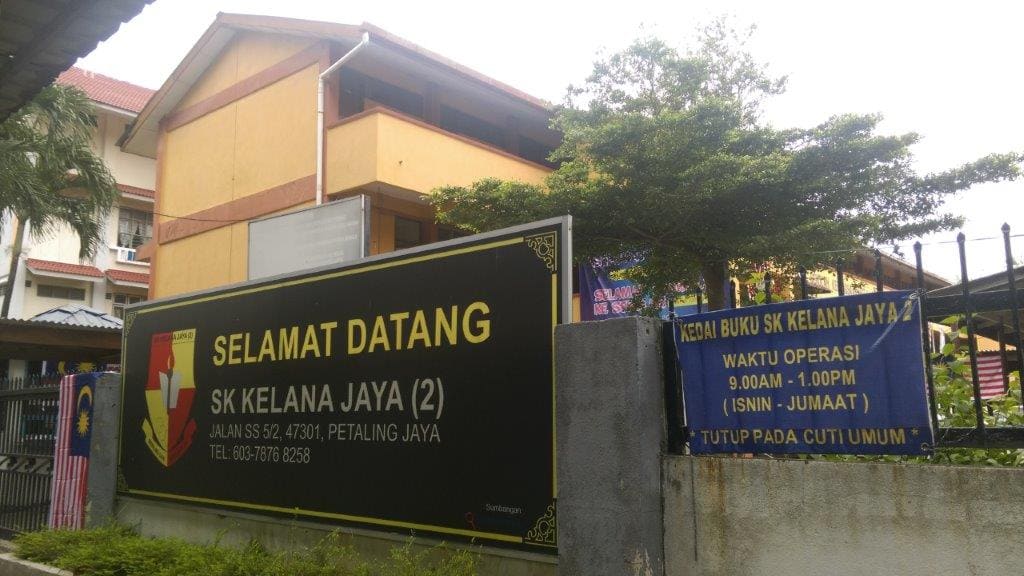
As Japan prepares to host visitors from around the world for the 2020 Summer Olympics, a Tokyo sports and cultural events company has launched a mosque on wheels with the hope that it would make Muslim visitors feel at home.
Yasuharu Inoue, CEO of Yasu Project commented that the possibility that there might not be enough mosques for Muslim visitors in 2020 is alarming for a country that considers itself part of the international community. “The Mobile Mosques have the added benefit of travelling to different venues as needed. As an open and hospitable country, we want to share the idea of ‘omotenashi’ (Japanese hospitality) with Muslim people” he said.
The back of the modified 22-tonne truck flips up to reveal an entrance and when the sides are slid out, the width of the truck doubles. The 48 square metres room can accommodate 50 people at one time. Muslim visitors can pray comfortably inside the mobile mosque, with taps and an outdoor washing area for pre-worship cleaning.
“Going forward, I would be so happy if people from Indonesia, Malaysia, Africa, the Middle East and, for example, refugees who are coming from Syria are able to use the mosque as a tool to promote world peace” Yasaharu concluded.
Plus Malaysia Berhad (PLUS) has ceased all operations on its mobile workshops (Workshop On Wheels). The service will no longer be available on all its highways.
The mobile service, which was first introduced in October 2012 with Automobile Association of Malaysia(AAM) was aimed at safeguarding motorists from being fleeced by unscrupulous tow truck and workshop operators. It also provided on-the-spot repairs and a free 24-hour towing service for up to 35km on the highways. Over the years, Workshop On Wheels has definitely helped reduce the number of complaints on unethical tow truck operators.
PLUS however, will remain to provide assistance to its highway users. Users are advised to follow the steps below:
Step 1:
Call PLUS Traffic Monitoring Centre (TMC) via the toll-free line 1800 88 0000 to speak to TMC and provide details and location of the vehicle breakdown.
Step 2:
TMC Officer will then assign a PLUSRonda response team to attend to the user immediately.
Step 3:
Wait for the arrival of the PLUSRonda response team.
Step 4:
PLUSRonda team arrives. Upon inspection, should the vehicle need to be towed, the PLUSRonda team will seek the driver's permission to tow the vehicle to rest area, toll plaza or any nearest safe locations.
Step 5:
If the vehicle cannot be towed and the response team is unable to repair the vehicle on site, PLUSRonda personnel will seek the vehicle owner's permission for the vehicle to be towed and fixed by registered agents whereby all costs will be borne by the owner.
Step 6:
TMC Officer will once again call the user to seek confirmation if the assigned response team has arrived and identify any further assistance that can be provided.
PLUS also wishes to advice the public to beware of any suspicious individuals who claim that they are assigned or sent by PLUS to provide towing or repair services on the highways. Highway users are encouraged to contact PLUSLine for any suspicious services offered by any third-party tow trucks and agents.
Meanwhile, PLUS is actively looking at collaborations with various third parties to introduce other emergency highway services to provide added values to its users of its hig
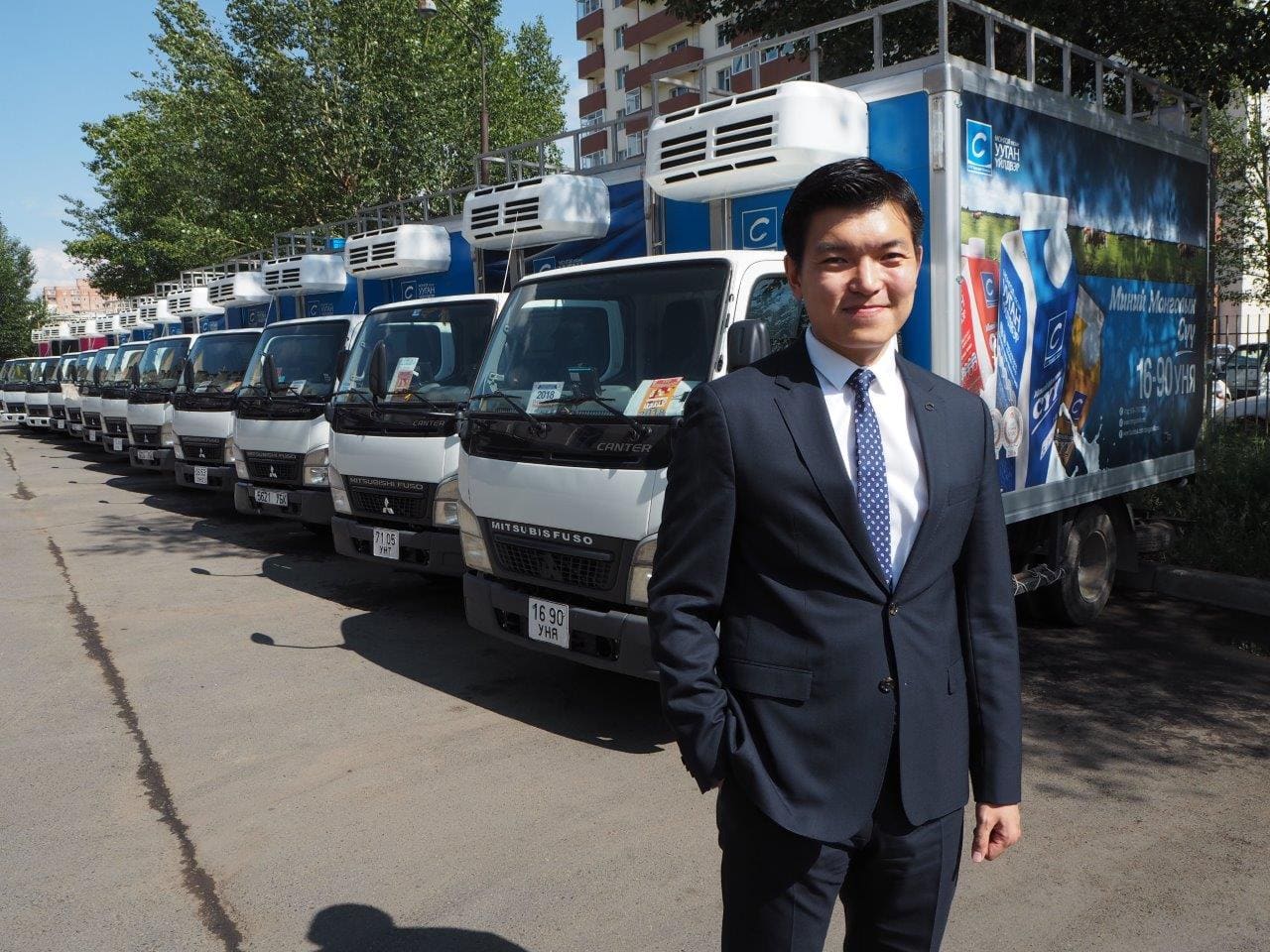
Axscend combines engineering, sensor technology and electronics expertise, together with software programming. The company develops solutions to digitally manage trailers in a comprehensive manner, enabling fleet operators in achieving notable cost reductions and higher fleet efficiency.
With the patented Trailermaster Connect connectivity solution – an intelligent interface for line connection technology and usually equipped with a telematics unit – each semi-trailer can be upgraded or retrofitted to a smart trailer with extensive data-based capabilities. This technology also allows for data transfer and analyses even when the trailer is uncoupled, enabling fleets to make the most of their resources. Key features that can be integrated include lighting function control, load monitoring and optimization, maintenance condition checks, tire pressure monitoring, EBS data evaluation, patented performance data and an evaluation of braking system performance (which relieves testing in the brake test center in the UK) and GPS data transmission for trailer tracking. Several thousand trailer licenses have already been sold to fleet operators under a license-based model.
SAF-HOLLAND sees an ideal opportunity to combine Axscend’s technology with its own chassis systems, particularly for brake system performance monitoring. SAF-HOLLAND expects intelligent applications for trailer management to meet increasing interest from major fleet operators in Europe and North America and sees significant growth potential for Axscend’s technology in the years ahead.
"This technology acquisition is right in line with our Smart Steel innovation campaign, which is driving us to make axles smart and provide for the digitization of trailers. We are increasingly integrating sensors and electronics into our mechanical components and are working on issues such as the automated coupling of tractors and trailers in addition to preventive maintenance. Axscend makes trailers intelligent, and its expertise – particularly in the software area – will contribute noticeably in speeding up our development work even more," explains SAF-HOLLAND CEO Detlef Borghardt in his comments on the acquisition.
CFO Dr. Mathias Heiden adds: "Digitalization offers us a tremendous opportunity. Besides gaining valuable know-how and technology input we are also interested in Axscend’s subscription-based business model, which has already been a success. This will be an important building block for complementary as well as completely new data-based business models."
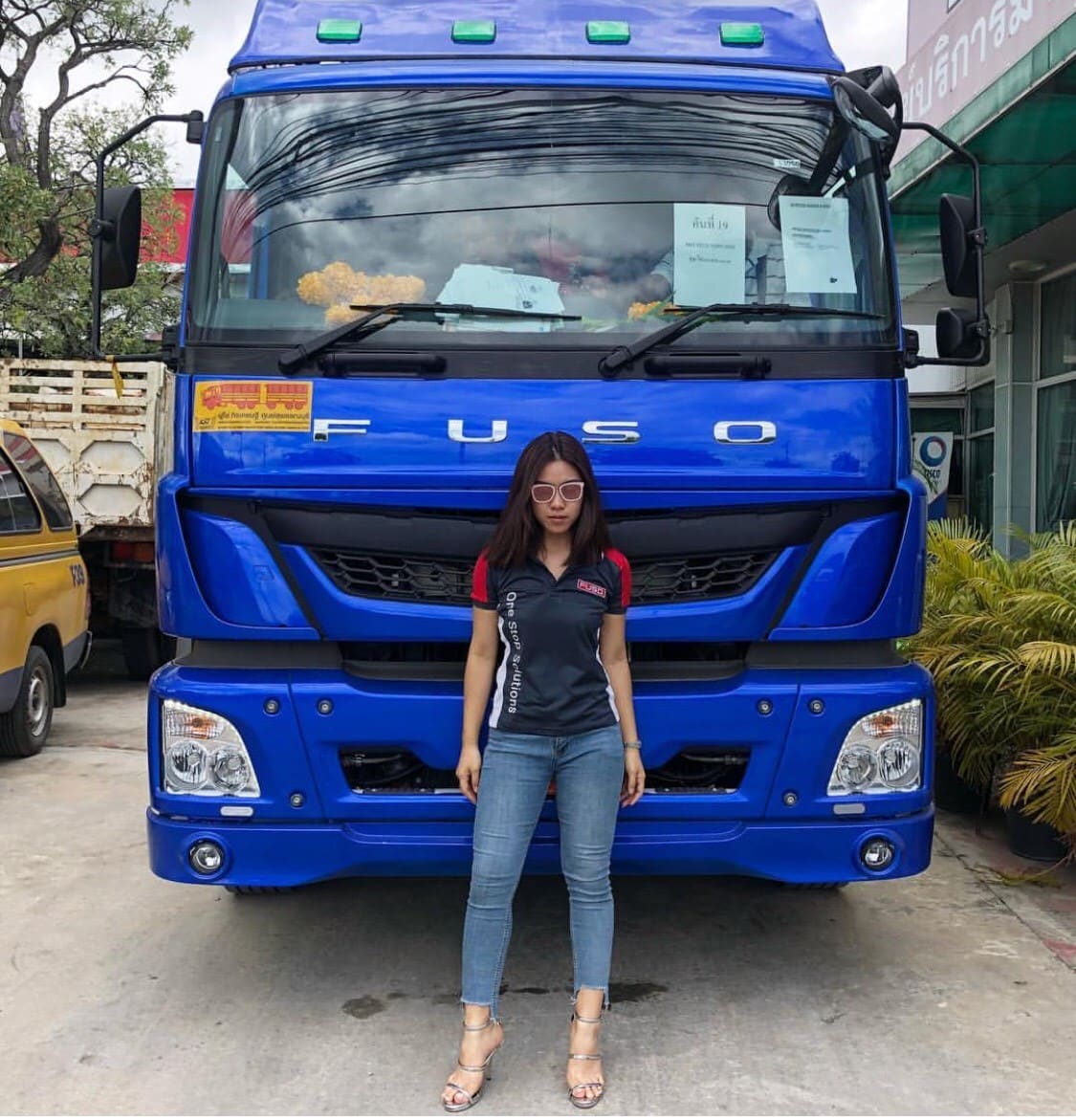
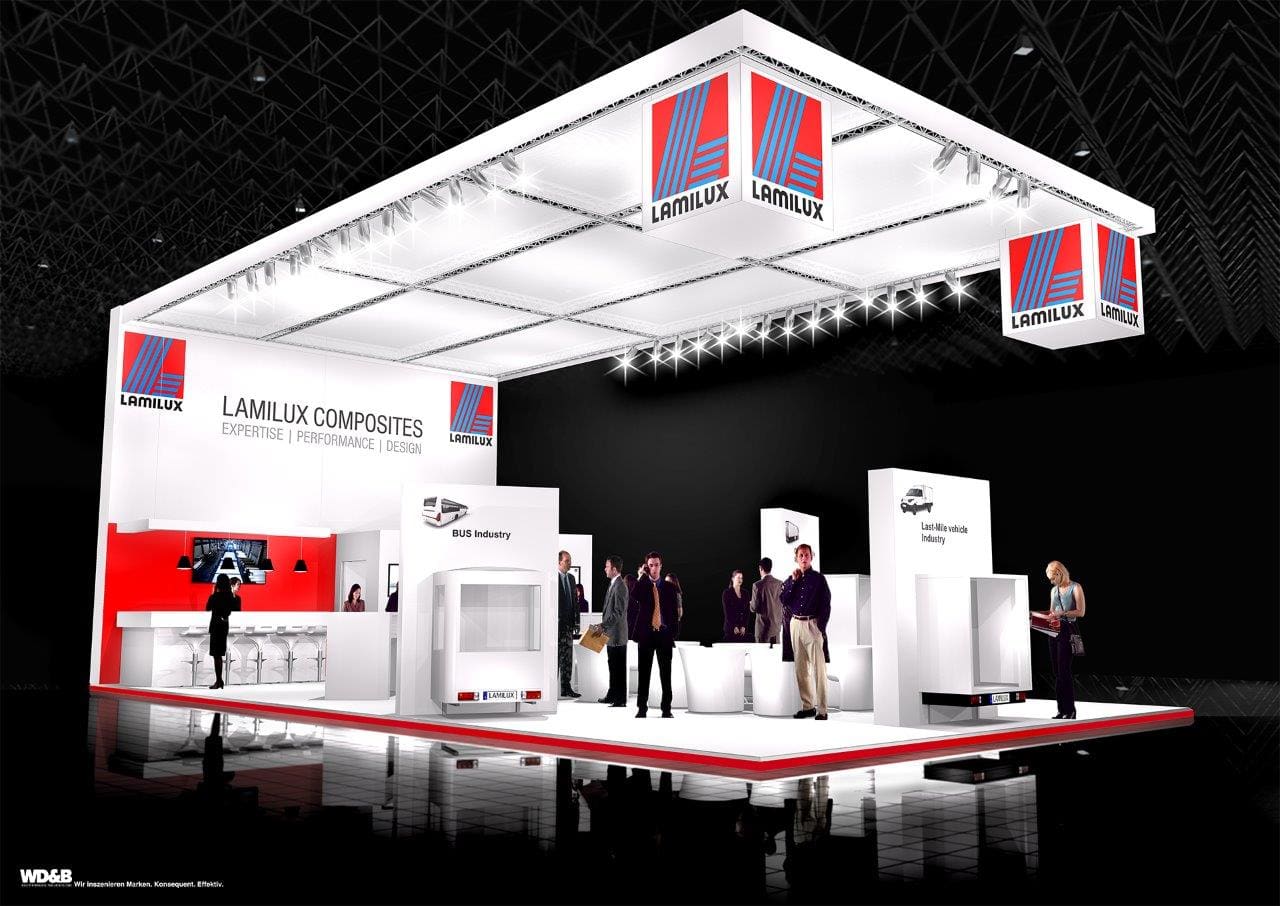
The new LAMILUX Anti Slip PES Clean Grip incorporates a special granular aggregate to withstand harsher and even more persistent loading conditions. This makes the anti-slip flooring even more robust. Its service life is extended, while the functionality of the material remains unchanged.
The use of LAMILUX X-treme in last mile vehicles ensures considerable savings in weight while nonetheless allowing the construction of extremely robust superstructures. In sandwich constructions or as single sheet, this composite material sustainably reduces the fuel consumption of the vehicles.
Three demonstration models will be exhibited at the LAMILUX stand: the applications of the GRP products will be demonstrated using truck, bus and last mile vehicle models. For lorries, the materials used are High Impact with AntiBac surface, the non-slip flooring AntiSlip and the food-safe HACCP material Woven Roving 48% Plus SH for interior walls. In the case of buses, LAMILUX demonstrates its flair for design: LAMIfoamtex with its soft-touch surface, Composite Floor, which resembles laminate flooring, and LAMIGraph, for interior cladding, are the proven materials of choice here. And for roof applications, the manufacturer presents its robust and long-lasting Woven Roving 48% Gelcoat SH.
All LAMILUX products are designed to satisfy a number of requirements at the same time. They always offer at least 2-in-1 or even 3-in-1 benefits. This means that LAMILUX GRP, for example, combines a harmonious appearance with robustness and durability, and reduces processing costs and the number of processing steps for customers at the same time. “The added benefits are the hallmark of our products: we’re familiar with the application situations of our customers and produce the ideal products to satisfy their requirements”, says Markus Bächer, Head of Marketing. “In this respect, we consider it our job to keep on developing: to serve the customer, whatever the challenge.”
Unplanned downtime due to breakdown or urgent repair means significant costs, both time and monetary. This could be avoided with well-planned service and repairs and this is where the Volvo Service Planning comes in handy.
With the Volvo Service Planning feature, customers' uptime is guaranteed. Pre-booking with this service allows Volvo's service advisors to ensure a bay is booked with the technician and parts on standby, all ready to go when customer's truck enters the workshop for its scheduled maintenance and repairs. This helps get customers' trucks back on the road in a timely manner.
"We have a system that lets us plan our customers' truck maintenance schedule," said Law Ah Tiong, Volvo Malaysia's Aftermarket Vice President. "All our dealers use Volvo Service Planning to schedule their customers' maintenance. We track their mileage through a system and send them emails or short text messages to inform them when it's time for service, about seven days prior. We suggest to them which workshops to go to depending on their locations," he told Asian Trucker in an exclusive interview recently.
With the aim to allow customers focus on their main businesses, Law said it is important for trucks to be maintained regularly, which is why after every few thousand kilometres, Volvo service advisors will actively call customers to schedule their service slots.
"This way, they (customers) do not need to worry about missing a service or late maintenance because there is a team that is already keeping track of when their vehicles need servicing," Law said. The service advisors will also ask whether the customers need any additional repairs or attention to their trucks. This is a proactive step on Volvo's part, so they can put technicians, bays and parts on standby.
Maintaining close engagement, service advisors will tell the customers how long their trucks or buses' downtime will be, so the customers can arrange backup vehicles for their businesses, hence uptime can be ensured.
Besides dealing with trucks and buses, Volvo also hoped to raise awareness on punctuality among its customers. "We want to educate them on being punctual when it comes to bringing their vehicles in for scheduled maintenance. If they come late, they will have to wait much longer as we would have others to attend to," Law said. Volvo had done roadshows to raise awareness in May, but it will not stop there as they want to have a continuous engagement with customers.
The Volvo Service Planning is exclusively for customers under the Volvo Blue and Volvo Gold Service Agreements.
Volvo Service Planning: Step by step
1. The right input |
4. Keeping you updated. |
All relevant information about your truck is entered into the system. This includes the truck’s exact specifications, how it will be used, the expected distances involved, and much more. |
Volvo will contact you 7 days before the actual service due date to make an appointment with your nearest dealer. A reminder will be sent 2 days before the appointment date for your team’s peace of mind. This simplifies fleet planning and you know that each truck is getting the right service. |
2. Identifying the best solution. |
5. Fine-tuning your service. |
Volvo determines the right level of maintenance for your truck and develop your Individual Service Schedule. |
When your truck is with Volvo, they fine-tune the Individual Service Schedule if new data shows that this is necessary. This ensures optimal maintenance for best possible truck performance and fuel efficiency. |
3. Precise planning. | |
The Individual Service Schedule shows exactly when your truck needs a service and what actions need to be performed. |